Interflux ICSF Select6
Selective jet fluxing for soldering
Introduction
The Interflux ICSF Select6 selective jet fluxer equipment delivers a high-speed, high-precision method for applying flux in both wave soldering and selective soldering processes. This machine is engineered to optimize the flux amount at each soldering point, ensuring the expected cycle time even during high-volume wave soldering operations.
With the ICSF Select6, the entire flux application process becomes manageable, meeting the increasingly stringent and complex soldering requirements of today, especially for lead-free processes. This system also offers significant flux savings, improved product cleanliness, and enhanced reliability.
Product options
- Oversized boards software option
- Nozzle Type Jet nozzle, 186μm hole size – NEW high speed, high precision jet valve
- Nozzle Quantity Single or double (option, for 2 different fluxes) jet nozzle
- Nozzle Material made of stainless steel, PEEK, PPS, sapphire with EPDM seal material
- Flux types ALL types; water based, water soluble, alcohol based, rosin based, …
- Flux Jet Control Patented flux drop check by laser guarantee the correct application of each drop. (Optional)
- Flux Programming Options Dots, lines, multi-lines, and areas. Parameters can be set for each individual dot, line or area
- Flux Tank Stainless steel, 10 or 3 liters
- Tank Quantity 1 or 2 (optional), additional tanks with or without couplings for quick tank exchange also available
- Barcode Options Different barcode options are available for automatic program selection, program verification and traceability applications. Optional
- Traceability Option Industry 4.0 ready. All process values are available in text file reports and an SQL database. Optional
- MES Interfacing Customer specific modules interfacing the traceability software (SQL dB) with Manufacturing Execution System software can be developed. Optional
- Double Nozzle (optional)
- Conveyor with 3,5° angle (L-R or R-L) – optional
- Laser sensor for flux jet detection (optional)
- Preheater (for selective soldering)
Parameters
- Product Size, L x W 610 x 610mm or 920 x 610mm
- Dimensions, W x D x H 1,000 x 1,240 x 1,670mm
- Weight 600kg
- Machine Frame Welded
- Conveyor Type Horizontal or slanted (option) SS316 5mm pin chain conveyor
- Conveyor Length 1,000mm
- Conveyor Height SMEMA height 930mm ±30mm
- Conveyor Width Automatic adjustment by software: Max 610mm
- Conveyor Speed Incoming/outgoing: 10 to 300 mm/s (separate software setting)
- Pass Through Direction left to right or right to left. Software setting, NO mechanical change over
- Product Positioning Patented soft stop with 2 step detection by Laser Sensor (No mechanical Stopper)
- Safety circuit with front and back emergency stop buttons, front and back door with individual contacts and feedback to software. CE certified
- Power Supply 1-Phase, 200-240V AC, 50/60Hz, 13A
- Compressed Air Supply Compressed air NOT required
- Exhaust Requirement Exhaust NOT required. 100mm diameter exhaust connection available
- XY Linear Axis System High speed, high precision, servo-controlled belt drive
- Speed Max. 1,500mm/s
- Accuracy ±0.25 mm
- Repeatability ±50 μm
- Maximum Solid Content 40%
- Flux Supply Patented variable flow, volume and pressure system with supply pump and NEW high speed control valve
- Flux Flow Variable for each programmed location on the board. Controlled by software setting and flux supply pump
- Flux Volume Variable for each programmed location on the board. Controlled by software settings, valve controller and high-speed flux valve
- Flux Pressure Manually adjustable pressure setting
- Flux quantity control Through valve opening time: 0.35 to 10 ms. The flux quantity is also related to the flux type and properties.
- Flux Nozzle Cleaning Automatic, programmable flux nozzle purging to prevent nozzle clogging
- Flux Quantity Measurement Software function for accurate flux quantity measurement. A separate precision weighing scale is required.
- Flux Level Detection Contactless low-level switch and alarm for each tank
- Flux Tank Drain Automatic drain of supply system and tank by software function with operator prompts
- Machine Software PLC controlled, can run independently from the PC Software in case PC breaks down
- Programming Software Windows 10/11 PC with Flux Designer software package, with on and offline programming, picture editing and machine control
- Programming device PC with Microsoft Windows 10/11 operating system
- User Security 3 user levels, each with defined access level and a programmable user list
- Programming Base Point and click programming. JPEG, BMP, GIF, DXF picture import. For CAD and GERBER files a screen print is recommended
- Picture Editing Editing software integrated in main software: four-point stretch, rotation, mirroring, brightness & contrast control
- Flux Library Database with default programming values for each type of flux
- Flux Programming Functions Copy, paste, copy with base point, rotation, line up, zoom, etc.
- Program Optimization Software function to optimize flux application routing
- Flux Mode Standard (stop & clamp, highest precision) and continuous (no stop, highest throughput) fluxing modes
- Alarms and Events Current alarms, alarm history, software events, machine events and security events
- Remote Support Remote support for PLC and programming software available worldwide via TeamViewer
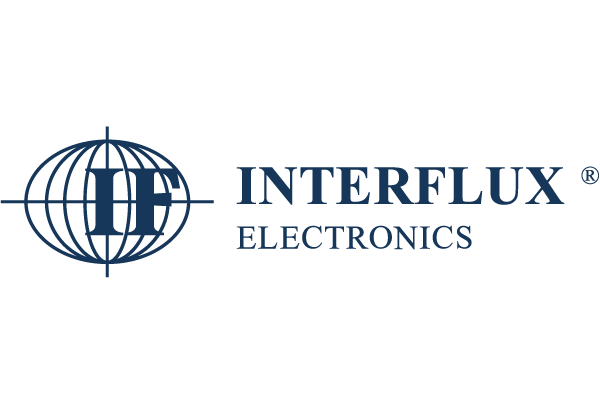
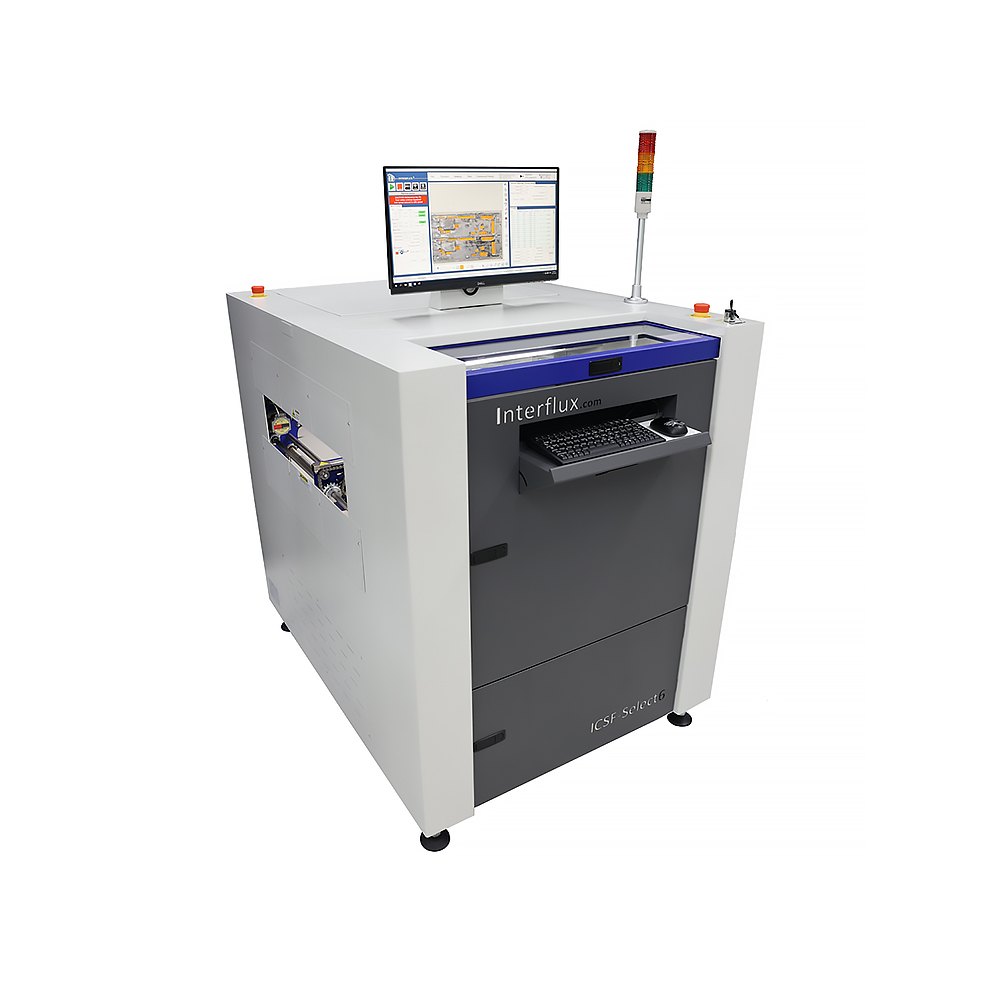